ブーミレバー構造でよくある失敗は何ですか, そしてそれらをテストする方法
科学オリンピックの競技会がもうすぐ始まります! チームが設計を収集し、過去数年間で最高のパフォーマンスを発揮した構造をレビューする時期が来ました. ことし, 私たちは、Boomilever が失敗する理由と、組織を強化するために何ができるかをより深く検討したいと考えました。.
ブーミレバーの設計
SkyCiv で構造物をモデル化しましたか?? 最初にこの記事を読むことから始めることをお勧めします: SkyCivでBoomileverを設計する方法. 最初の構造をモデル化して設計し、ブーミレバーのパフォーマンスをシミュレートする方法を示します。 前 あなたがそれを構築します!
次の記事では、構造をテストして分析する方法について説明します, モデルの問題を事前にシミュレートして発見できるようにするため.
私たちのデザイン
デザインの最も重要な部分はメンバーを配置する方法です. トラスを使うつもりですか? トラスのどのようなスタイル? これは、負荷がかかった状態での構造のパフォーマンスと全体の重量の両方に最も大きな影響を与えます。. それはあなたがしなければならない唯一の最も重要な決定です.
記事上で, 次の簡略化された設計に基づいて設計を進めます。:
これは次の要素で構成されます:
ソース: ブーミレバー Wiki
あ: サポート/ベース
B: テンションメンバー
C: 遠位端
D: 圧縮クロスメンバー
それでは、これらのメンバーが失敗する可能性があるさまざまな方法をすべて確認してみましょう, デザインの強化にどのように貢献できるか.
失敗例
圧縮失敗
圧縮力とは、 圧縮する メンバー, または 打ち砕く 内側へ.
使用できる失敗基準を選択したいと考えています. 私たちの記事から、 バルサ材の圧縮破壊応力はおよそ 7 MPa. 木材は異方性を持った素材なので, 強度は木の質と木目の方向によって決まります, ただし、故障ストレスの仮定は、この設計で使用するための良い経験則になります。
私たちの目標は、すべての圧縮部材の圧縮応力が次の値以下になるようにすることです。 7 MPa. 純粋な圧縮が原因でメンバーが失敗する可能性は低いです。, しかし、これは理解しておくべき重要な概念であり、以下のチェックにとって重要です。.
張力の失敗
引張力とは、 テンション メンバー内で, または 外側に引っ張る
バルサ材は引張強度が圧縮強度の 2 倍です. 純粋な引張力によって構造が破壊される可能性は非常に低いです。. これは失敗基準として無視できます.
障害チェック
1. 曲げ応力破壊
よくある失敗例である曲げ応力から始めます。. その名のとおり, これは、部材が中立軸に対して垂直に荷重されると発生します。 (NA) 曲がり始めます, 部材の断面に沿った応力の分布を引き起こす. 曲がりが発生している明らかな兆候, 特に木材の場合, 部材がそのスパンに沿って元の形状からたわむ場合.
私たちの場合には, 積み込む前はすべての木製部材が真っ直ぐである, したがって、たわみがあれば、部材が曲がっていることがわかります。. 曲げ応力を受けたメンバーは次のようになります。:
メンバーの上部が圧縮されている (-) そして一番下 (+) 緊張している. の “M” この場合に応力分布を引き起こす正のモーメント力です。.
曲げの失敗を特定する方法
Structural 3D でブーミレバーの解析を実行した後, 後処理から作業していきます, または 解決ウィンドウ. 使用できます 可視性の設定 画面の右側で、いくつかの表示/フィルタリング オプションを求めるプロンプトが表示されます.
私たちの目標は、曲げによる圧縮応力が以下を超えていないことを確認して確認することです。 7 MPa. 権利を使用してください 結果の可視性 上記を超える応力を表示するオプション 7 MPa:
このタイプの失敗は次のビデオで見ることができます。:
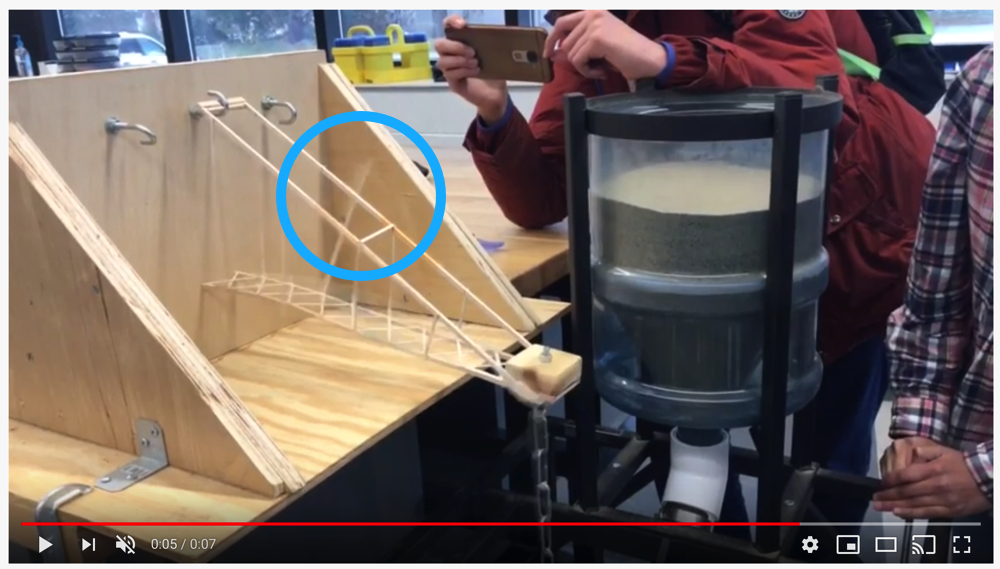
このビデオでは、引張コードと圧縮コードを接続する支柱が、曲げと座屈の組み合わせによって破損することを示しています。. これは、主要な障害点がこれらの接続にあることを示す上記のモデルと一致します。.
曲げ破壊に対する強化方法
ここでは、曲げ破壊が起こりやすい部材が 4 つあることがわかります。 – 負の値が圧縮限界を超えているため、 7 MPa. これらの弱いメンバーを特定したので、, セクションの高さを増やすことで強化できます:
メンバーの高さが増加すると、慣性モーメントが増加します, 断面強度に直接関係する断面特性. この場合, メンバーの身長が上がるにつれて, 曲げ応力が減少します, およびその逆. 同じ木片を曲げようとしていると想像してみてください。, しかし、この 2 つの形状では, どちらの方が壊れにくいでしょう?
この変更を行うことで、曲げ力によって生じる応力の量を最大約 6.7 MPa.
別のオプション, クロスメンバーを追加して、他のメンバーに力を分散させます。. これは構造に重みを加える可能性があるため、オプションよりも常に好ましいとは限りません 1 (複数のメンバーのセクション サイズと重みを増やすこととは対照的に、1 つのメンバーを追加することの違いを考慮する必要があります。. この場合, 構造を強化するためにブレース部材を追加しました:
円式の慣性モーメント, 1 つのブレーシング メンバーが 3 つのメンバーに沿って力をより均等に分散するのに役立ったと付け加えました。. 相手側のメンバーの過度なストレスも軽減しました (から削減 -7.31 に -4.895 MPa). ただし注意, 示されているように、これにより構造内の対称性が破壊されます。.
このブレースメンバーのパターン (またはトラスメンバー) あなたのデザインに依存します. ここにあるいくつかの トラスの種類 そして彼らの長所と短所.
2. 座屈破壊
これは細身の人にとってよくある失敗です, 薄いメンバー. 座屈 高い強度が発生した構造部材の故障モードです。 圧縮性 突然の横方向のたわみを引き起こす応力. そんなふうにメンバーを押し倒すことを想像してみてください, それから キック 出てそのまま崩れる:
ブームミレバーの場合, 部材の長さに対する断面寸法の相対的な比率により、部材は座屈しやすくなります。. ソフトウェアで座屈解析を実行することで、座屈をテストできます。 解決する. これにより、モデルをチェックして、座屈の危険にさらされているメンバーがないかどうかを確認します。:
アラートが示唆するように, より小さい数値 1 座屈を示します. したがって、私たちのブーミリバーは現時点では座屈には大丈夫です. 座屈の問題があった場合, 構造上では赤いメンバーとして表示されるため、重要なメンバーを特定して設計を変更できます。.
注意: 科学オリンピックのタワー競技会ではコラムメンバーが多いため、座屈は特に重要です.
3. 接続/サポート
基礎と重要なつながり (あなたの遠位端のように) 事前に設計する必要もあります. 設計のこの部分が構造の成功を左右する… 文字通り! まずは支持層を見てみよう. これにより、張力のある 2 つのメンバーがメインボードに接続されます。. 構造の基礎部分に欠陥があってはなりません. これに関して助けが必要な場合は, 参照する ブーミレバー設計に関する Aia のガイド, 重さ約 1.5g でサポート力に優れた効果的なベース設計に関する優れたガイドが記載されています。 18-19 kg.
TL; DR
ブーミレバーの故障箇所を特定するには、以下を確認することをお勧めします。:
- を超えるストレスを特定する 7 MPa. を切り替えます。 ストレス ストレス制限の結果 7 これらを識別するための MPa. メンバーが失敗したら, あなたが試すことができます:
- 断面積を大きくする
- ブレースメンバーを追加する
- 構造の形成またはトラスのスタイルを変更する
- 座屈解析を実行する (特に柱または垂直部材の場合) より大きい値を探します 1
- メンバーの長さを短くする
- 断面積を大きくする
- 途中でブレースメンバーを追加します
- しっかりとした基礎を身につけてください, それが失敗の原因であってはなりません
- もしそれが, 強力なベースデザインについては、Aia のガイドをご覧ください。.