In this version of Industry Insights, we interviewed Gordon W. Bartlett, Structural, Petroleum Engineer and CEO of G.W.Bartlett and Associates LLC. Gordon has an extensive track record with materials, so is able to speak quite well on the idea of "Light Weight Technology" (LWT) as it relates to structural members and design. This Q&A will showcase his experience and dive into the what and why of Light Weight Technology.
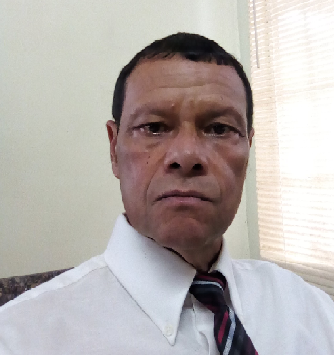
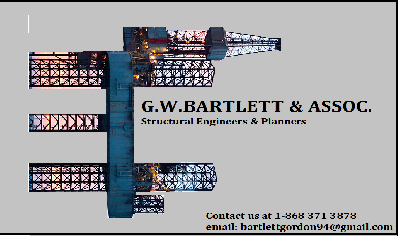
Gordon Bartlett
CEO of G.W.Bartlett and Associates
Gordon exemplifies dedication to education: he has a B.Sc in Chemical Engineering and Ph.D. in Petroleum Engineering focusing on Structural Dynamics of Crude Oil Production. He is a retired Professor of Chemical and Petroleum Engineering and has over 40 international publications on the subject matter. Professionally, Gordon was a former Crude Oil Production Engineer, a Research Consultant, as well as a Chief Energy Consultant to the Trinidad and Tobago government.
His focus has been on developing LWT for warehouse and manufacturing construction. This has allowed him to design and deliver affordable housing for low income families in the Caribbean.
Light Weight Technology basics
Q: What does Light Weight Technology mean?
A: Our meaning of "Light Weight Technology" is a technology or branch within Structural Engineering that utilizes any steel section or system that can attain equal structural strength to that of traditional steel sections with a corresponding decrease in weight of more than 50 percent. It must be noted that currently, each section type of traditional steel systems (e.g. H,I,L and T sections) is more than 500% heavier than each member of the LWT section for any given specific surface thereby allowing for significantly improved handling logistics during field operations.
For example by using a combination of two C-Purlin sections each having a weight of 3.93 lbs/linear ft, it is possible to construct a section-system having equal bending strength to that of a traditional I-section of weight of 25.4 lbs/linear ft..
Q: How is the industry currently using LWT?
A: A review of engineering materials literature indicates that these LW materials are being used in the construction industry as structural support materials, for wall bracing (studs), roofing supports (rafters) together with limited use between traditional heavy steel sections and/or reinforced concrete in already existing structures for repairs requiring low or zero structural integrity.
Most commonly, LW sections have been used as single members only for support of high structural capacity sections and have not been structurally combined or fabricated for specific construction activities which require higher structural integrity than that for which they were designed.
It is important to note therefore, that LW members have not been used to replace wide flange sections or S beams but more as secondary members supporting and/or distributing loads to the more structurally dominant primary load bearing members.
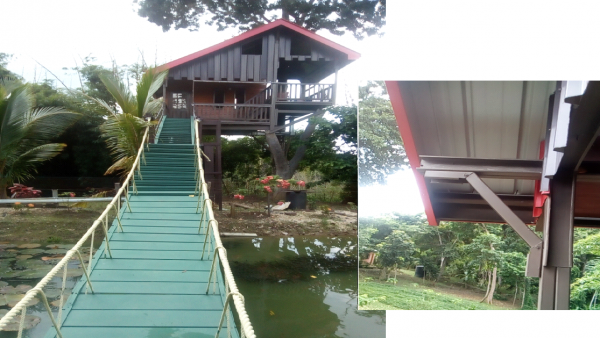
Mountain top tree house construction using entirely LWT. Roof beam/column/gusset design shown on the right
Thoughts on the current and future state of the industry
Q: Where do you see this unique industry going in the next 5 years?
A: Over the next five years the industry will be driven by the market for lower-cost residential, commercial and industrial construction. Accordingly, where C-purlins (the primary section used for the on-site fabrication of I and H-section columns, piles and beams) now ranges between 1.2 and 1.5mm in thickness, the industry will move to increase the thickness up to possibly 2.5mm and greater. In addition to C and Z- purlins, purlin manufacturers will add more geometric shapes to their line in order to improve area-inertia properties.
As these improvements take place, the structural load bearing capacity of these members should increase, thereby allowing the industry to replace more costly traditional sections with lower cost LW sections. The overall effect should drive down the cost of construction and cause construction projects previously deemed uneconomic to be ventured as an economically viable.
For example: An I beam fabricated on-site without welding using 2.5mm thick steel C-purlins will then have second moment of inertia equal to that of a comparable heavy steel section and will have a weight savings of close to 200%.
The effect of these endeavors will hopefully give rise to expansion of the industry over the next five years.
Q: What techniques are engineers using to design these LWT sections?
A: Immediately, the research capabilities of SkyCiv come into focus, whereby the engineer can maneuver the geometry and axis orientation of a single purlin with respect to another and investigate the resulting effects of these changes. Thus, in designing a single I-section from the combination of 2 similar or dissimilar C-purlins, or a truss section from the combination of a number of C-purlins, the engineer can study the effects of changing LW section specifications and environmental conditions (wind, rain, snow, earthquake etc.) on moment of area, load bearing, deflection and bending moment.
The SkyCiv platform reports generated from these analyses will eventually direct on-site fabrication for customizing the LW section members. The final step of this series of calculations from the SkyCiv platform is to optimize the weight versus the structural integrity of each section member, thereby minimizing the cost of construction through the reduction in $/lb. of steel utilized in the construction process.
Q: Are the LW components made with any special materials? Are these materials readily available?
A: The good news is that these LW components are not made with any special materials. Standard hot dipped galvanized low carbon steel sheets varying in thickness between 1.2 to 1.5mm are formed into LW components utilizing the cold forming process in most cases . These forming processes are well established and codes for standardized bolt and screw connections are well documented in the structural engineering literature.
Low carbon steel is currently readily available in all countries who themselves purchase from the world's major steel suppliers (US, Brazil, India and China).
Two-story luxury oceanfront under construction using 100% LWT; Unique pile/column/floor beam connections shown on right
What are the pros and cons of LWT?
Q: Other than reduction in weight, what are some of the positives of the LWT innovation?
Most of the positives of this innovation are enveloped in the main theme of Light Weight Technology. However, some major indirect advantages include:
- Transportation and handling logistics of these construction materials are greatly reduced and can be handled by manual labor instead of heavy machinery.
- The increased cost savings resulting from utilizing this innovation has resulted in previously uneconomic construction projects being restarted as economically viable employment generators especially at the low to unskilled labor level.
- A notable spin-off from this is that the potential for employment of labor is enhanced especially in depressed economies where there is a great supply of low to unskilled labor. This can have a formidable impact on easing the increasing unemployment statistics in the construction industry in a post- COVID era where the IMF in its latest report on Latin America and the Caribbean have stated that for these regions of the world real income and employment will decrease until 2025, more than any other region. Post 2025, employment will increase marginally unless there are vigorous efforts by world leaders to prevent this. Structural Engineering by way of LWT is therefore an obvious contributor.
- This LWT innovation has already started to cause an increase in home and agricultural DIY projects. Additions, replacements and repairs are on the increase with a corresponding increase in demand for the light weight structural members.
- Where safety is always the major concern on any construction site, accidents involving lost time, injuries and even fatalities will decrease as the use of lighter weight construction materials increase. In fact, OSHA statistics indicate that 20% of all worker deaths are in the construction industry and of that figure 28% is caused by: i) being struck by or pinned beneath heavy steel and ii) being squeezed by or between heavy steel. LWT can play its part in reducing these figures.
Q: Are there any drawbacks to these light weight sections?
- The first limitation is the current ability to undergo large scale construction involving large live and dead loads. For example high rise structures in excess of 5-stories, industrial vessel construction and long span bridges are obvious limitations.
- Currently codes for the use of LWT are either limited or unavailable in the wider structural engineering literature as its use has not been well or fully established. With time and continued use the industry will develop such.
- Software packages for its use have not been yet developed as the technology is driven by custom designs for specific projects. The analysis of the structural integrity of beam members for custom geometries requires engineering first principles which are now accomplished by the very tedious mathematical models for each section member which is usually non-standard. Computer packages to assist in the design are therefore lagging the use of the technology.
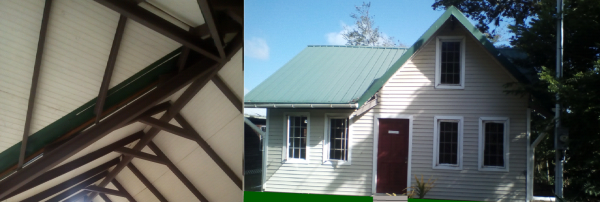
Hillside Cottage Utilizing LWT; Gable Roof Truss Design on left
What would you say is the overall impact of LWT on the structural engineering industry?
This technology essentially utilizes light weight steel sections to achieve the load bearing capacity far in excess of that for which they were designed. This has allowed the industry to extend the use of these sections from its original role of providing support to reinforced concrete and traditional sections to creating lightweight combination sections capable of providing stand-alone structures at significantly reduced costs. This has been a major impact on the industry.
By critically investigating the intrinsic parameter of surface area per unit weight of steel sections, the SE Industry can expand the use of design parameters such as Ixx, Iyy and Izz to achieve LW combination sections with the structural capacity to withstand far greater loads with correspondingly greater structural stability.
Purlin manufacturers are therefore expanding their tooling to provide the structural engineering marketplace with purlins of increased thickness and varying geometries to lessen the amount of on-site fabrication required for custom section designs.