Aluminum I-Beam Strength Calculator
Aluminum beams are a common material for construction projects due to their lightweight yet durable properties. However, understanding the load capacity of these beams is crucial for ensuring the safety and integrity of the structure. To help with this, many online resources provide aluminum beam load capacity charts and calculators. These tools allow engineers and builders to quickly determine the load capacity of an aluminum I-beam based on its size and configuration.
To assist structural engineers in determining the load capacity of various aluminum beams, SkyCiv has built a free aluminum i-beam strength calculator, with some limited free access. This tool allows engineers to input the dimensions and properties of the beam and receive a calculation of the load capacity based on industry standards. There are versions of the aluminium capacity calculator available for:
- Australian Standards - AS/NZS 1664 Aluminium Structures
- United States - ADM-2015 Aluminum Design Manual
- Europe/UK - Eurocode 9: Design of Aluminium Structures (BS EN 1999-1-1 )
- Canadian Standards - CSA 157-17 Strength Design in Aluminum
This is a preview of our full version aluminum design software, which also includes the following premium features when you subscribe to either our Quick Design Module or SkyCiv Professional:
- Premium: Integration with SkyCiv's analysis software for more comprehensive analysis.
- Premium: Full results, no lockouts.
- Premium: Full reporting capabilities and analysis of multiple load cases for accurate assessment.
- Premium: Advanced bending analysis, support for various beam configurations, and a user-friendly design for ease of use.
About the Aluminum Beam Capacity Calculator
What does the Aluminum Beam Capacity Calculator check?
The SkyCiv Aluminum design software, offers powerful and detailed design checks as per four design standards. These standards include AS 1664, ADM-2015, BS EN 1999-1-1 and CSA 157-17. So the user can provide simple input and receive quick and clear results back. Although each standard if different, the aluminum tool includes checks for:
- Shear checks (in both directions): Calculating the beam's shear strength and comparing it to the applied design load.
- Bending checks (in both directions): Calculating the beam's bending strength in both directions and comparing the result to the design load.
- Tension Checks: Calculating the strength in tension and the utility of the design based on user inputted design loads.
- Compression Checks: Calculating compression in columns for axial, gross section, and the minor axis.
- Combined Checks: Calculates relevant combined checks such as combined compression and bending, combined tension and bending or combined shear compression and bending
These checks are essential for ensuring the safety and integrity of the structure, as they help to identify any potential weak points or failure modes that could compromise the column or beam's load capacity.
Aluminium Design Software
The above aluminum calculator is a simplified and limited version of SkyCiv's full aluminum design software. While the calculator provides a comprehensive analysis of the beam's load capacity and performs checks on the aluminum section for shear (bi-axial), bending (bi-axial), compression, and tension, the full software offers a more comprehensive set of features and capabilities for aluminum design. Including:
SkyCiv's Aluminium Design Software, includes a full integration with SkyCiv's Structural 3D Analysis software:
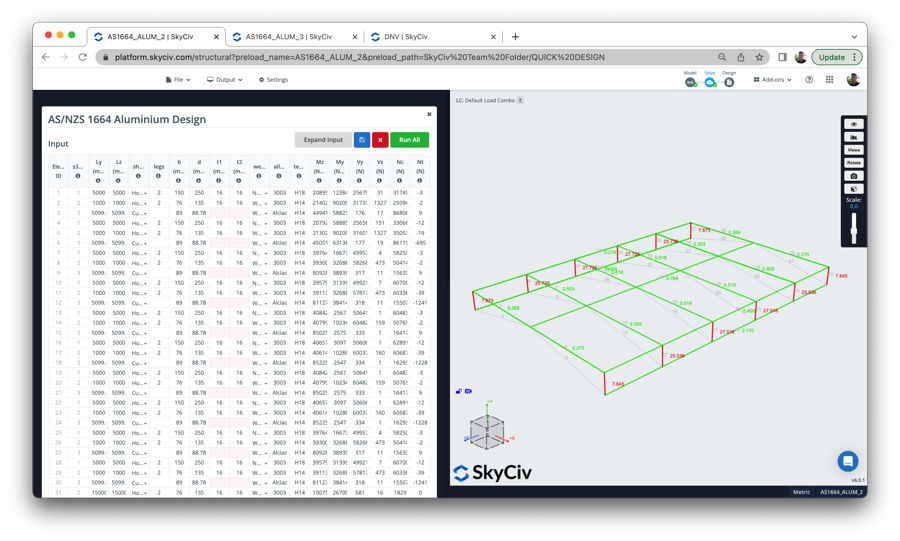
The above software also includes detailed and comprehensive design reports which make it easy for the engineer to trace the calculations of the software allowing you full transparency of your calculations. These are very handy if you're looking for an aluminium design example, or want to double check your designs, as the full calculations are displayed. These design reports are included in the premium version, which show clear and comprehensive aluminium design reports:
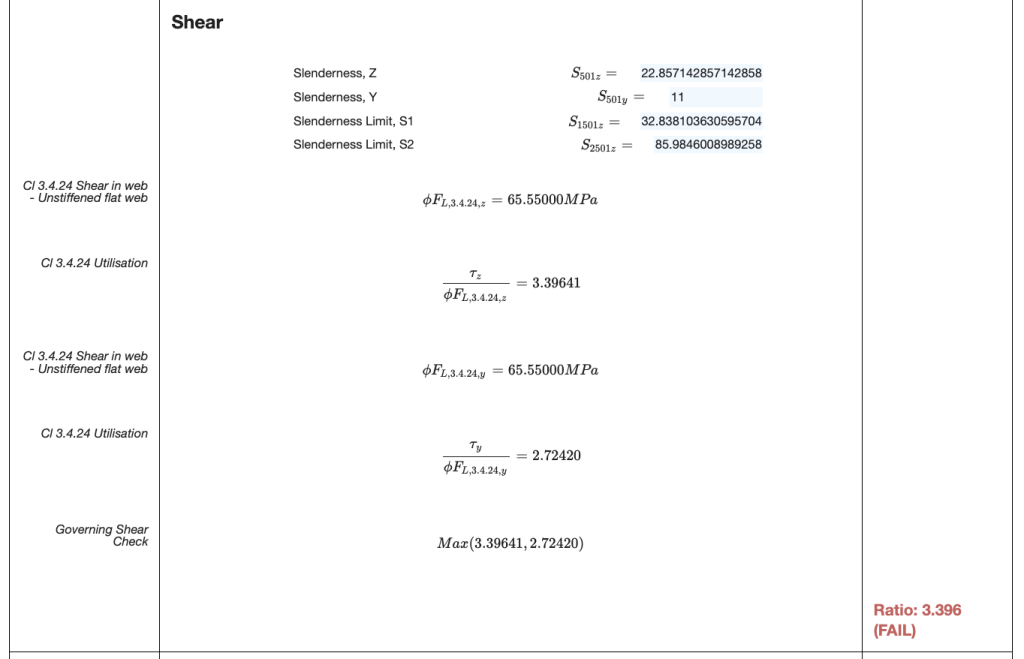
What determines the capacity of an Aluminum Beam?
Aluminum beam capacity is determined by several factors, including:
- Material: The strength and type of aluminum alloy used to construct the beam play a major role in determining its capacity.
- Section Dimensions: The width, height, and shape of the beam cross-section also play a role in its capacity. A wider and taller beam will generally have a higher capacity than a narrower, shorter one of the same material. Obviously, the section thickness also plays a critical role in the member's strength. Experiment with the above calculator to see how dimensions affect the capacity and utility.
- Span Length: The span length of a beam, or the distance between its supports, can also affect its capacity. As the span length increases, the beam will have to support more weight and become weaker, particularly to buckling and compressive forces.
- Load Concentration: The type of load applied to a beam can also impact its strength and overall capacity. For instance, a point load, which is a concentrated load applied at a single point, is more challenging for a beam to support than a uniform load since there are considerable shear concerns as all the force is concentrated at a single point. Distributed loads are, as defined, distributed. So more of the material is being used to support the load.
- Load Application: The manner in which the load is applied to the beam can also play a role in its capacity. For example, a beam that is loaded from the top will have a different capacity than a beam that is loaded laterally. For shapes such as I beams, this will be reflected in the member's strong and a weak axes.
What is Aluminum Design?
Aluminum design is the process of designing aluminium elements such as beams or columns. Aluminum is a common design material due to its versatility, strength, anti-corrosion advantages and lightweight nature. It can be easily shaped and molded into complex and custom shapes which makes it suitable for a wide range of applications.
To perform aluminum design, engineers need to assess the strength of the element and determine whether or not there is sufficient capacity to withstand the required design loads. These could be loads from wind, snow, dead loads and live loads. Engineers generally either use hand calculations or software to perform these calculations.
There are a few steps in designing aluminum beams. It usually starts with identifying the load and span requirements before moving onto selecting the appropriate size and type of aluminum beam. Finally the engineer will determine whether the member is strong enough for the required design loads. Here is a more detailed overview of the process:
- Determine the load and span requirements: The first step in designing aluminum beams is to determine the required loads and required span of the beam. This includes calculating the expected loads (such as dead, snow, wind, live etc..) that the beam will need to support. These loads can be combined, or taken as final worst case design loads (such as in this tool). These factors directly determine the size and type of beam that will be required.
- Select the appropriate size and type of beam: Aluminum beams come in a range of sizes and shapes, including I-beams, H-beams, and rectangular beams. The size and shape of the beam should be chosen based on the load and span requirements. Tools like the one on this page, are a great resource for designing the beam. Users can specify different sizes and types and re-run the calculations to determine the utility of the member.
- Ensure proper support and anchoring: It is important to ensure that the aluminum beam is properly supported and anchored to prevent it from buckling or failing under load. This may include using additional supports or anchors at the ends of the beam, or adding bracing to the beam to increase its stability.
- Design considerations: These may include the overall usage or risk category of the structure, the environmental conditions the beam will be exposed to, and any additional features or requirements, such as corrosion resistance or fire resistance. For instance, aluminum is quite a corrosion-resistant material and good in applications where salt water is present. Additionally, aluminium is fairly fire resistance but by no means is it completely fireproof (aluminium will melt at around 660 degrees Celsius). These are all important considerations when deciding whether aluminum is the right material of choice for a particular design.
- Use design software: Such as this aluminium design tool (which is also integrated with our structural analysis software), engineers will typically use structural engineering software as a faster/more efficient way to calculate and design these members.
What are the advantages of Aluminum?
- Lightweight: Aluminum is much lighter than other metals, such as steel, making it easier to install or transport.
- Strong: Despite its lightweight nature, aluminum is strong and durable, making it suitable for use in a variety of applications.
- Versatile: Aluminum can be easily shaped and extruded into a wide range of forms and sizes, making it suitable for a variety of design applications. Particularly when working with glass installation.
- Corrosion-resistant: Aluminum alloys are corrosion resistant in atmosphere (not so much when submerged in water) which makes them a suitable application where it is exposed to damaging elements such as sea salt.
- Recyclable: Aluminum is usually 100% recyclable, making it generally more environmentally friendly than some other materials.
What are the disadvantages of Aluminum?
- Expensive: Aluminum can be more expensive than other materials, such as steel. However, this depends on the application and sometimes the benefits listed above can offset some of additional cost of using this material.
- Limited applications: Aluminum is not suitable for use in certain cases where the member is under high stresses or is exposed to high temperatures. Typically steel will perform better in such applications.
- Difficult to work with: It can be difficult to connect or join with other materials.
What design standards are available in the Aluminum Design Software?
SkyCiv Aluminum Design supports multiple design standards which can be accessed by using the flag icon at the top of the left side input panel of the software. Aluminum Design Standards supported by SkyCiv include:
- ADM 2015 Aluminum Design Software
- Eurocode 9 Aluminium Design Software
- CSA 157-27 Aluminium Design Software
- AS/NZS 1664 Aluminium Design Software
What shapes are supported by the Aluminum I-Beam Strength Calculator
SkyCiv Aluminum Design supports the design of Hollow Rectangular Sections, I Sections, C Sections and Hat Sections.
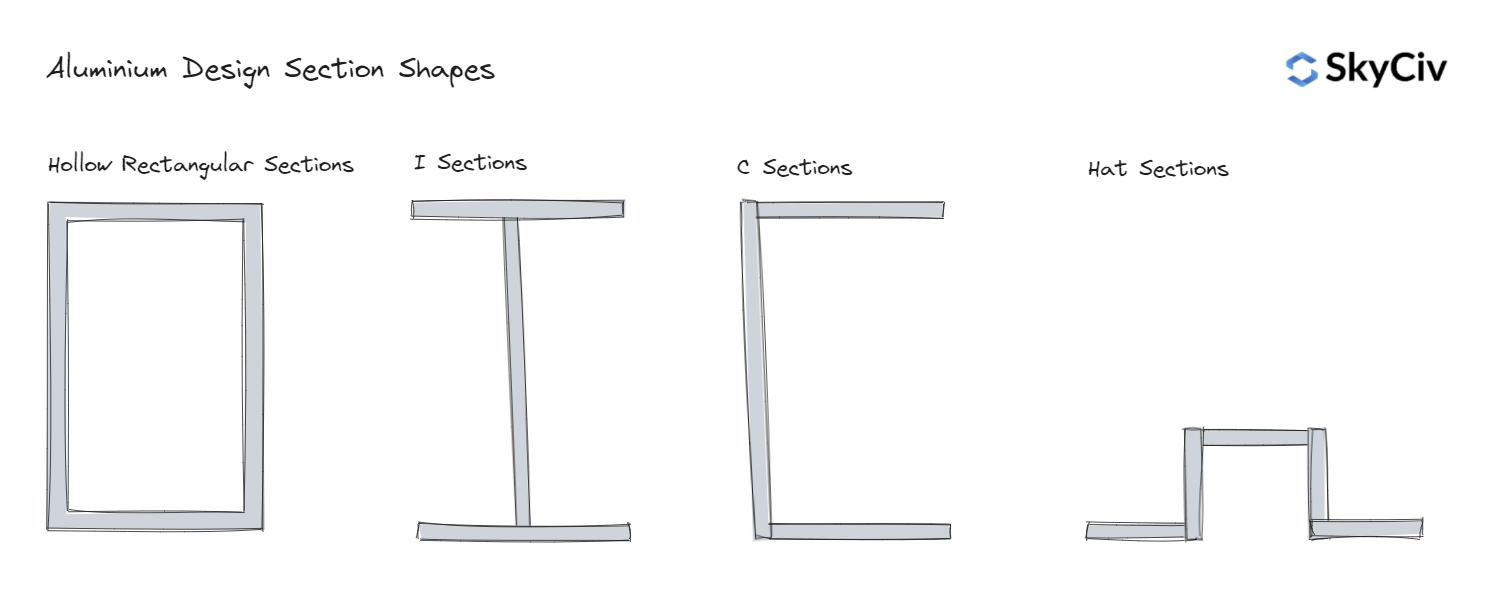
Aluminum Beam Span Calculator FAQ
The above calculator will calculate the section capacities of the aluminium section, based on your chosen standard. The capacity is determined from user input - including section dimensions, material properties, member length and braced conditions. Optional input for design forces are also available, users can specify their own design loads and the calculator will return the utility ratio for the each check.
The Aluminum Capacity Calculator requires inputs around the span of the member in both the z and y directions, details on the cross-section, welding, and material properties. Finally, the design loads are added to the calculator including major/minor bending and shear loads as well as axial compression and tension.
Yes, the calculator supports AS/NZS 1664 Aluminium Design, you can change the design standard using the related dropdown at the top of the left side input panel. Using SkyCiv Structural 3D, users can also import common materials from Welded and Non-Welded with a wide range of temper and alloy options. This means you can build, analyse and design your aluminium frames quickly and easily - combining our powerful analysis with quality design check capabilities.
Yes, the calculator supports ADM 2015 Aluminium Design, you can change the design standard using the related dropdown at the top of the left side input panel. The full version (integrated with our frame analysis software - SkyCiv Structural 3D) also includes a database of American Aluminum materials from the ADM database. This includes a range of products which can be easily searched and selected for design.
Yes, the calculator supports Eurocode Aluminium Design to standard (BS EN 1999-1-1), you can change the design standard using the related dropdown at the top of the left side input panel. Structural 3D (SkyCiv's analysis software) also supports a full catalog of European aluminium materials from a large database, for seamless material input.
Yes, the calculator supports CSA Aluminium Design to standard (CSA 157-17), you can change the design standard using the related dropdown at the top of the left side input panel. Our full frame analysis software also provides a full database of Canadian Aluminium materials from CSA S157-17 that can be easily imported into your model.
Structural 3D (S3D) is our frame analysis software. This module is integrated with our software, so users can build an aluminium frame, perform analysis on that frame, and then import all the loads, section properties and material properties to automatically check all your members at once!
A member's utility ratio refers to how much of the member's strength (capacity) is being used. For instance, if a member has a strength of 20kip and the applied load to that member is 10kip (based on live loads, dead loads etc..) then the overall utility is 50%. Generally, a ratio of > 1 represents a fail since there is more load applied to the section than it is capable of holding. Conversely, a ratio of 0-1 is a pass since since the strength is greater than the load being applied.
Related Tools
About SkyCiv
SkyCiv offers a wide range of Cloud Structural Analysis and Design Software for engineers. As a constantly evolving tech company, we're committed to innovating and challenging existing workflows to save engineers time in their work processes and designs.