Selecting Initial Sections
Start by modelling your usual structure, today we’ll be reviewing a model that has a Universal Beam for the beams, HSS sections for the columns and Equal Angle sections for the bracing. You can pretty much start with whatever sections you like, however we usually recommend selecting a section that you best guess will work. Here’s the model we’ll be optimizing:
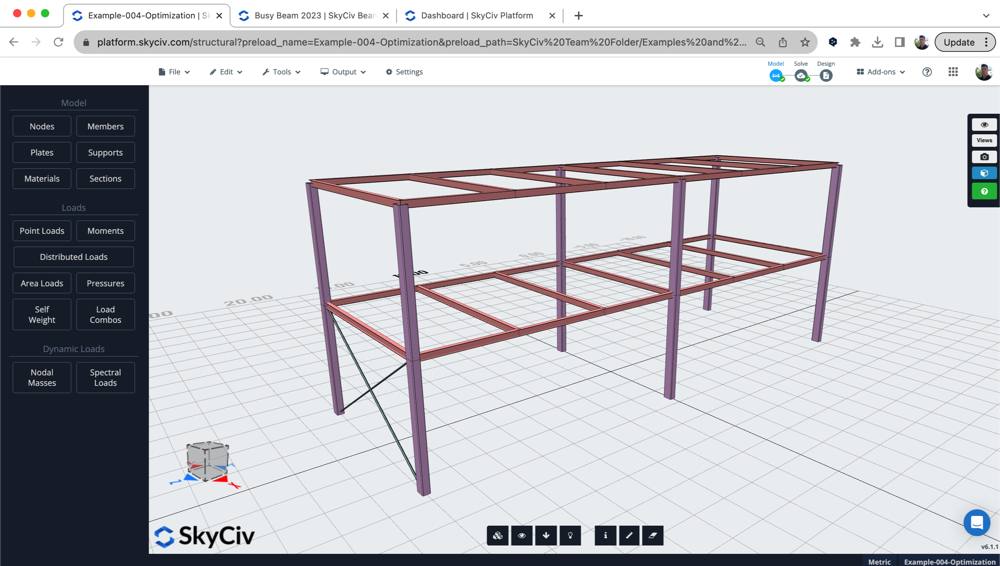
The model had load combinations, live/dead/wind loads and the proper restraints already setup. We also wanted to look at the initial material usage of this design. We use the 物料清单应用程序 to calculate the amount of material being used in the initial design:
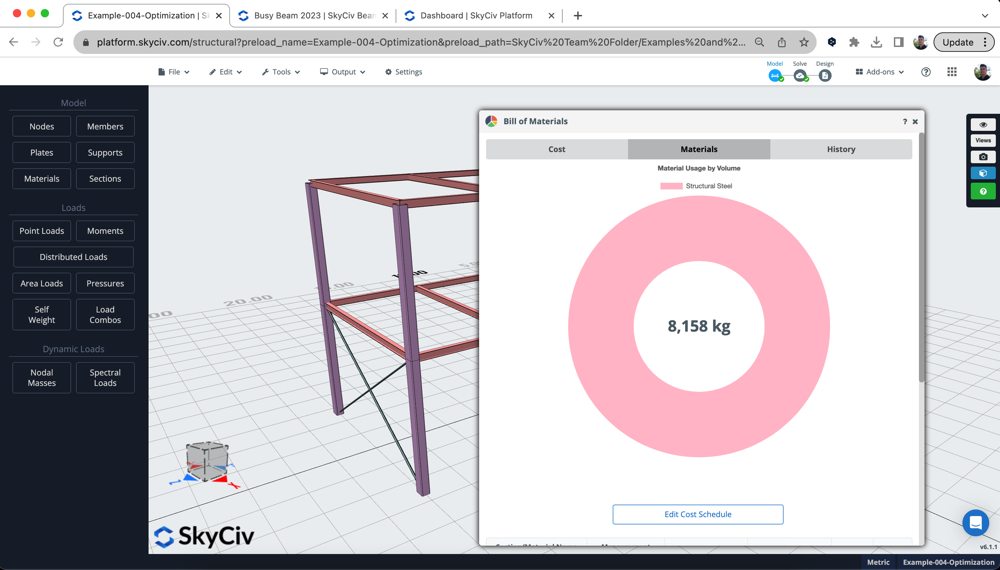
Review Design Results + Set the Settings for Optimization
It’s usually a good idea to review where the design is at initially by running the design check for the model. 在这个例子中, we’ll be using EUROCODE for the steel design check, but you can just as easily run the design check for the following:
- 钢 – AISC, CSA, 作为, BS, 是
- 木材 – NDS, AS1720
- 冷弯钢 – AISI, AS4600
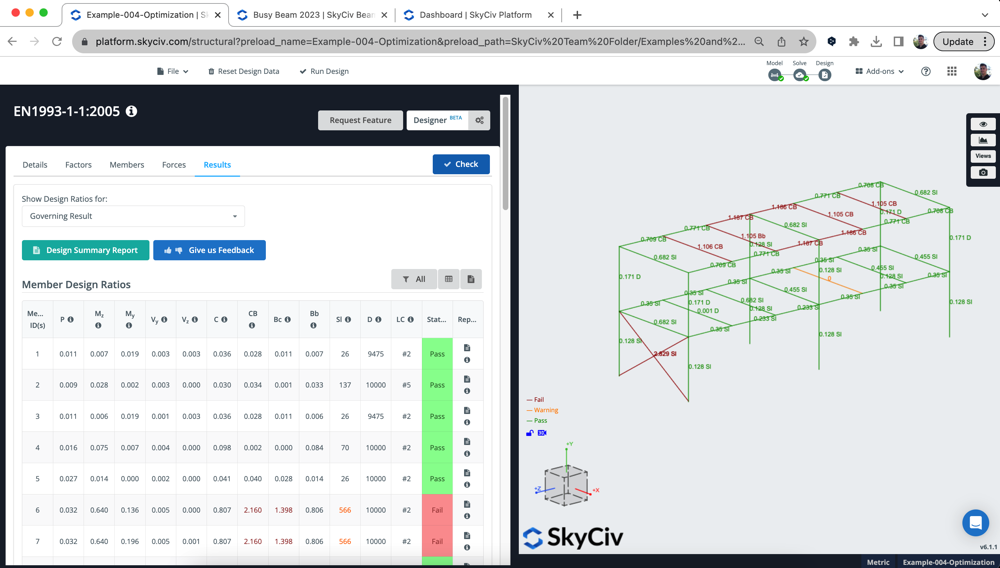
After reviewing the results, we could see the following:
- Universal Beams: Were failing, but only by a bit, with a utility ratio of about 110%. We want to optimize these to get them passing
- HSS Columns: were all passing, but very low utility (23%) so we felt we could optimize and reduce the material used here
- Bracing Members: these EA sections were all failing, with a utility of about 300%. We want to find the most optimal section that passed the design requirements
相应地, we wanted to run an Optimization using the Designer with the following settings. We want to design all 3 截面, with the analysis interval set to 0 (meaning the analysis won’t re-run after testing every section):
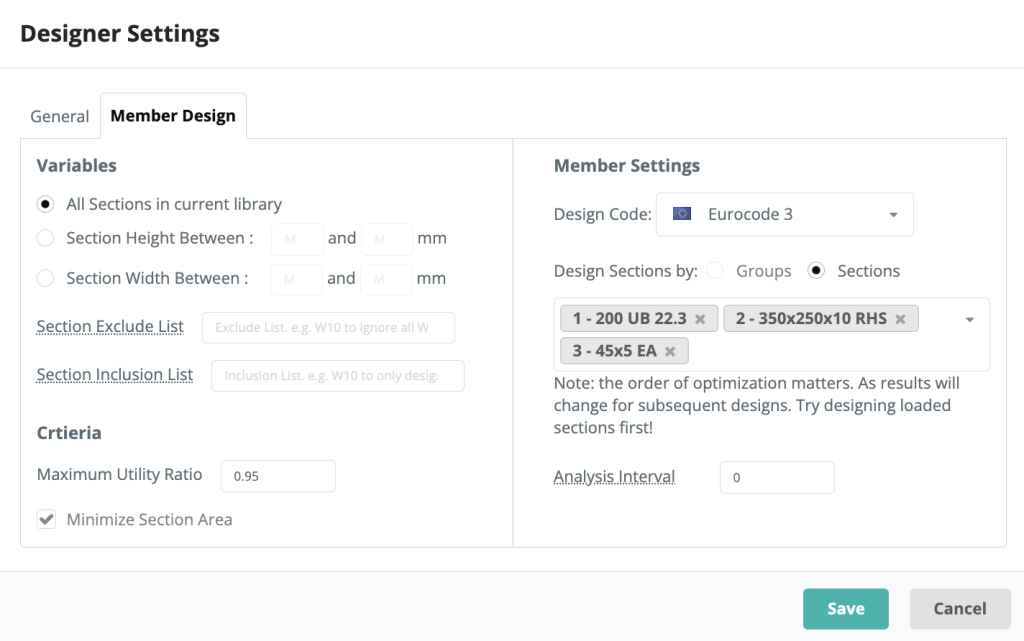
Reviewing the Results of the Designer
Once the designer runs, 我们收到以下弹出窗口 – 一目了然地显示所选的最佳部分:
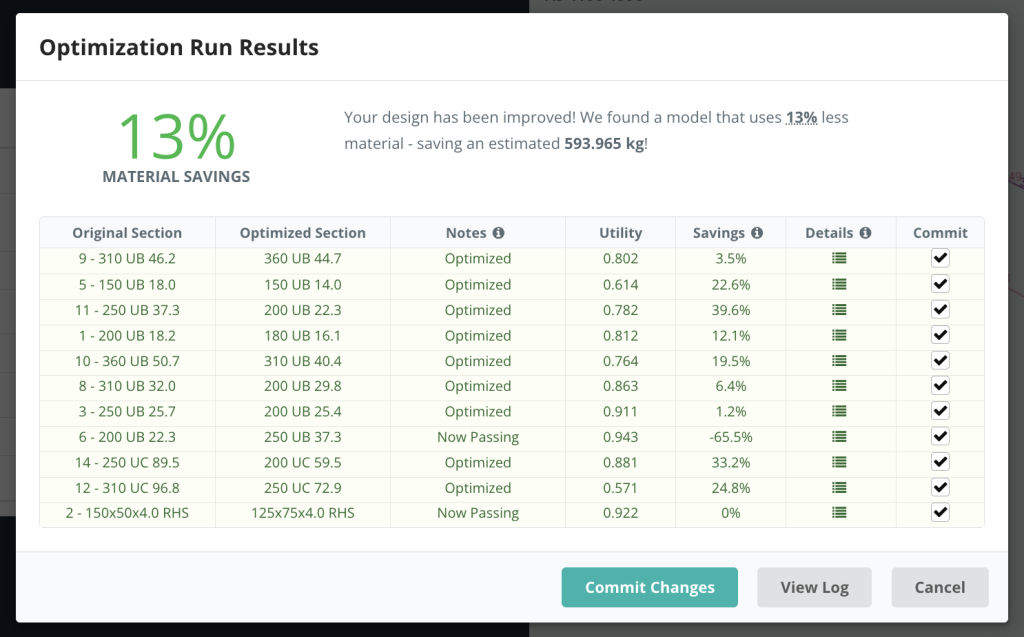
注意: the above screenshot shows the most up-to-date UI. Results are from a different model and do not match those in this tutorial
设计师能够为所有部分找到合格的结果. 结果如下:
- 部分 1 略有增加, 找到了一个可行的解决方案 94.9% 公用事业
- 部分 2 节占用大幅减少, 并能够找到一个可行的部分 88.6% 公用事业
- 部分 3 之前失败过, 现在经过一个更大的部分,但在以下位置进行了优化 83.2%
我们还可以通过单击查看每个部分的所有运行 迭代 图标. This will display more information on all the sections tested. 例如, looking at Section 2 above we can see it was only previously 22.9% utilized, and is not at 88.6%:
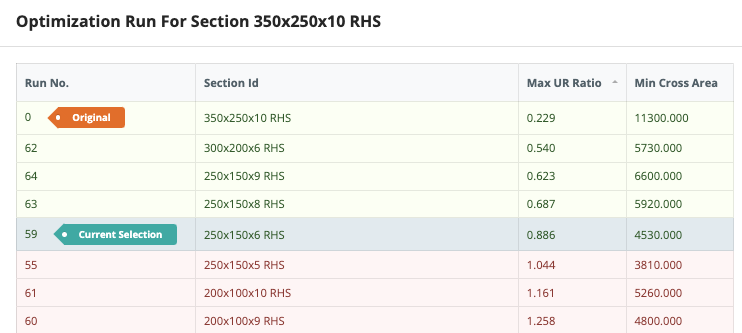
Committing Sections Suggested by the Designer
Once you’re happy with the proposed sections, 点击 提交更改. The software will then re-solve the model and re-check the sections. In our video, you’ll see the results not matching with the Designer for Section 1. This is because the 分析区间 was set to 0 – meaning the analysis results (特别偏转) 优化过程中未更新.
所以, 我们重新运行了 设计师 – 这次只是部分 1 并将分析间隔设置为 1. 再次提交更改后, 我们有一个完全设计的模型,所有部分都根据该设计标准进行了优化:
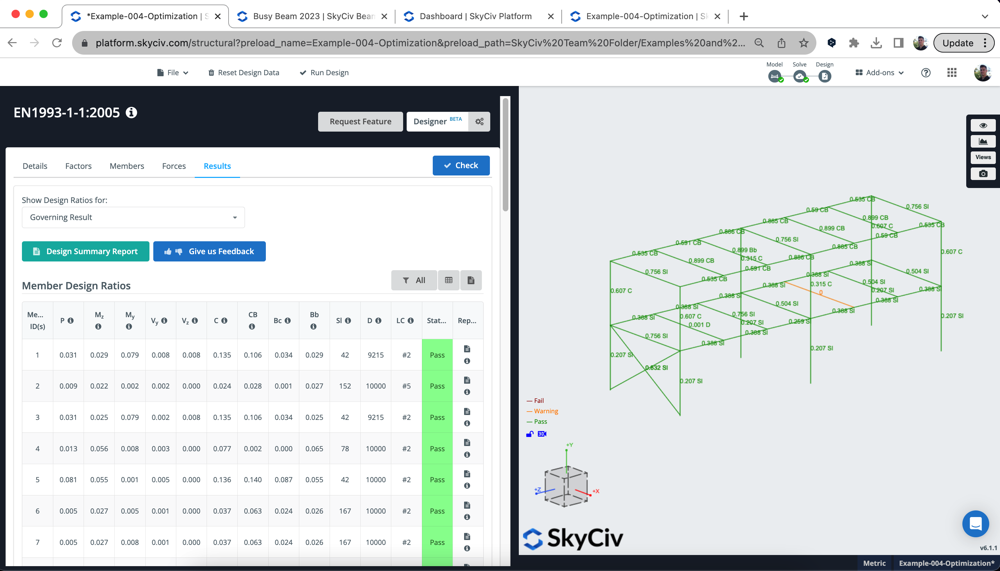
我们现在还可以使用第一步中使用的物料清单应用程序来查看成本节省情况, 这表明我们将结构模型减少了约2,000kg – resulting in almost 25% less material.
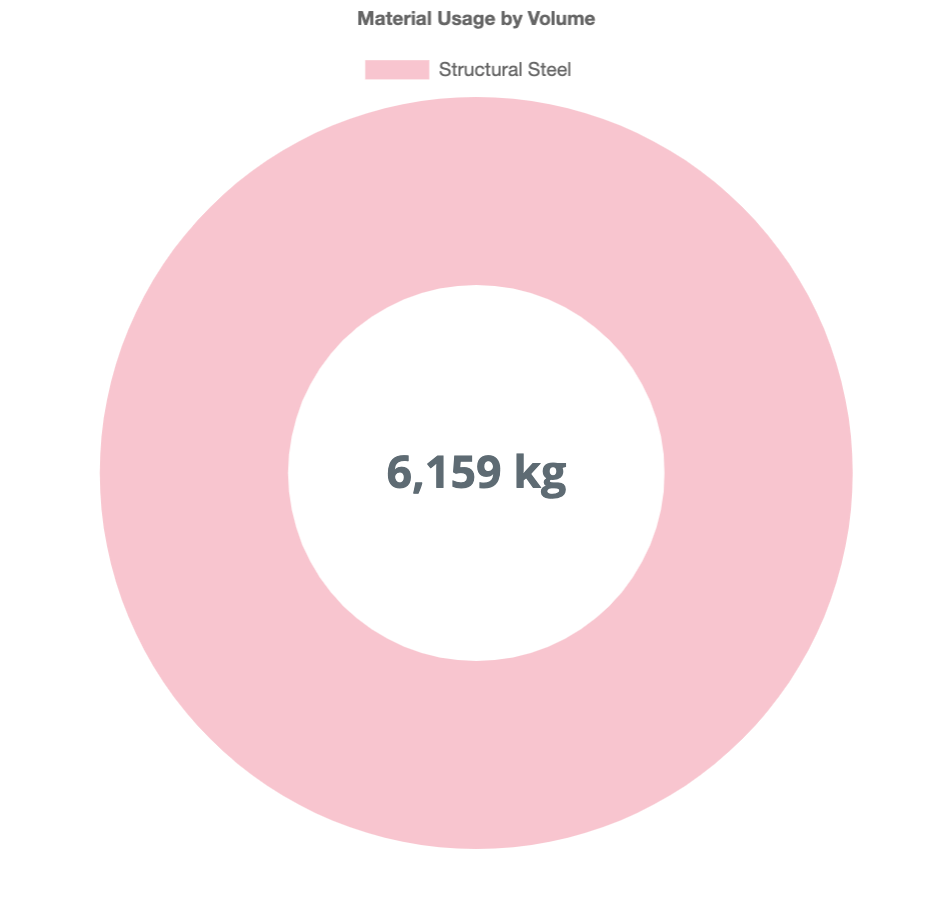
Optimizing Using SkyCiv Beam
We can also optimize single beams, using the SkyCiv Beam product. Combined with the above designer, we’re able to get quick and simple results for the optimal section. We can do this in 3 简单的步骤:
1. Build your Model – build your model the same way you always do, in this case we used a Canadian HSS section:
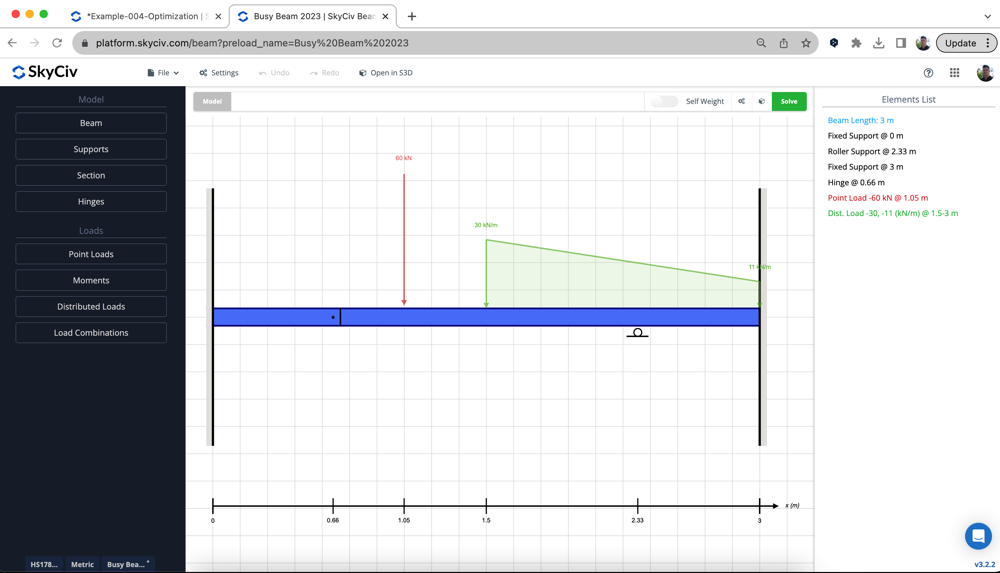
2. Review initial results – run Design (as per CSA S16 in this example) to see where our design is initially at. 在下面的例子中, the section is failing by about 20%:
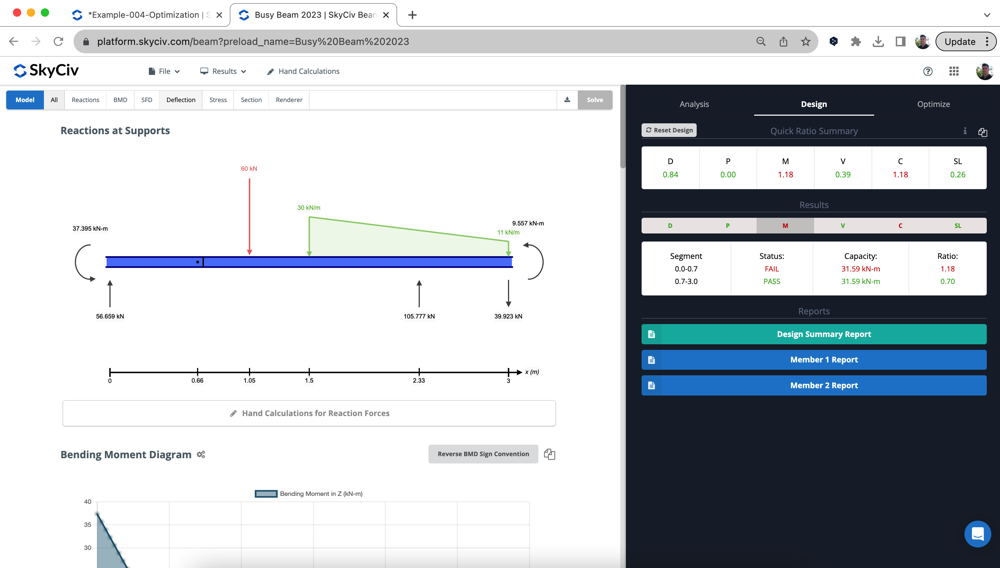
3. Run the Designer – run the Designer under 优化 with your desired sections and review your results. The most optimal section will already be selected, ready for you to commit to your model:

常问问题
We have two recommendations here:
- Large Models – Set Analysis Interval to 0 – 这会运行得更快并返回一些非常接近的结果. 然而, 结果可能不匹配, 因此可能需要第二次重新运行某个部分
- 较小的型号 – Set Analysis Interval to 1 – 这样您就可以获得最准确的结果,因为我们在每个横截面之间重新运行求解器
- 中等大小 – 设置分析间隔 t0 5 – 这将平衡对准确性和速度的需求.
Designer支持S3D中的所有成员设计模块, 包含:
- 钢 – AISC, CSA, 作为, BS, 是
- 木材 – NDS, AS1720
- 冷弯钢 – AISI, AS4600
对于 SkyCiv 光束, 上述所有的, 除风能模块外, 受到支持.