Experiment Conditions
Item | SkyCiv | CAD/FEA Analysis |
---|---|---|
Operating System | I7-6700 @2.6GHz - Mozilla FireFox | I7-6700 @2.6GHz |
User Proficiency | Intermediate | Intermediate |
Analysis Type | 1D Elements (Linear Static) | 3D FEA using ANSYS |
Software | SkyCiv Structural 3D | Solid Works / ANSYS |
Mesh Coarseness | Medium (25 eval points) | ANSYS Default Meshing Setting |
Time:
Item | SkyCiv | CAD/FEA Analysis |
---|---|---|
Software Loadup | 1 minute | 5 minutes |
Modelling | 12 minutes | 120 minutes |
Meshing | 0 minutes | 15 minutes |
Applying Loads | <1 minute | 3 minutes |
Solving Time | <1 minute | <1 minute |
Total | 0.25 hours (15 minutes) | 2.4 hours (144 minutes) |
Analysis Comparison
It was always going to be interesting to compare the results of the analysis - particularly as we are comparing apples with oranges. We are comparing the analysis of a simplified linear model VS a 3D model of joints, members and meshes. But obviously we want to make sure there is some degree of accuracy between the two methods. We found that the software results were within 7.4% of each other for peak deflection.Deflection Results
SkyCivCAD/FEA
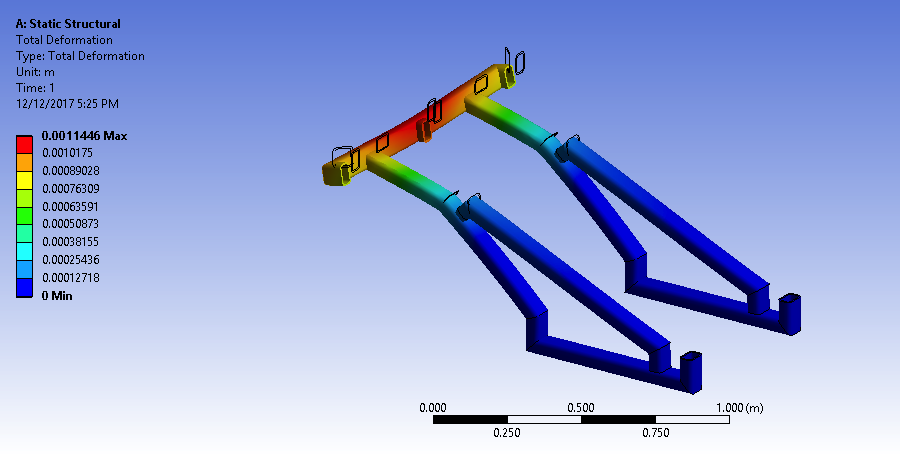
Summary
You could conclude that when looking at a frame analysis, the linear analysis software could produce results within an 8% tolerance of FEA software. This result took one-tenth the time to model, mesh and analyse. Two courses of action could be recommended:- Simplified Linear FEA took one-tenth the time to model and analyze
- Results were within 7.4% accuracy
- Use Linear software in place of CAD/FEA for these sorts of frames. Knowing that results will be within 8% accuracy (linear analysis is typically overstated)
- Use Linear software to come up with preliminary designs or double checks. Then finalize design using CAD/FEA models
Sam Carigliano
CEO and Co-Founder of SkyCiv
BEng (Civil), BCom
LinkedIn
CEO and Co-Founder of SkyCiv
BEng (Civil), BCom